When it comes to conveyor belt fastener selection, you’ve probably heard about “The Big Three,” namely: belt rating/tension, belt thickness, and pulley diameter. We’re such big fans of it over here, that we even wrote a blog about it. But that’s not the only thing that factors into your fastener decision. You have to think of the application and material you are conveying, the type of belting you are using, and even what metal will work best.
While it is pretty easy to line up what type of belting you have with your choice, and gathering information on your application is pretty effortless, what oftentimes trips people up is the metal selection. Will it be too hard and prone to cracking in the load zone? Will it be too soft and crumble in an abrasive application? Metal selection is a very important factor that doesn’t get enough press. So, let’s talk about it here.
Selecting the proper fastener is important. Use the filters on our Mechanical Belt Fastening Systems page to choose based on thickness, PIW, Minimum Pulley Diameter, and Application.
Why is metal type important?
If you’re looking to maximize the life of your fastener and prevent premature splice wear, fastener material must be matched to the application. The appropriate metal selection will deliver maximum performance in a variety of conditions – from wet and abrasive applications to highly corrosive environments. So there are a lot to choose from.
Let’s take a minute to review all the metals that are out there and where they work best, and in some cases, where they don’t work well at all.
Steel
Standard fastener metal that is not recommended for environments where corrosion can occur from acids and chemicals.
Galvanized Steel
Better rust resistance than non-plated steel.
Stainless Steel
Stainless steel provides extra resistance to abrasion and corrosion from acids and chemicals.
Everdur®
A corrosion-resistant copper and silicon alloy. Fully non-magnetic and spark free, low in resistance to abrasion. We also have a blog on how spark-free Everdur fasteners can reduce explosive risks a grain applications.
MegAlloy®
Features superior resistance to wear and abrasion. Extends the service life when compared to steel. Not recommended where impact or corrosion is a problem.
RustAlloy®
Low chrome stainless steel. Resists corrosion from mine water and other types of chemical attack.
Rubber-Covered Steel Top Plates: Some fasteners are available with rubber-covered top plates, for excellent resistance to abrasion.
At Flexco, we are consistently running tests on everything that has to do with our fasteners, including metal selection. Based on those tests, we have put together a chart that breaks down the important characteristics of each metal and included it below for your reference.
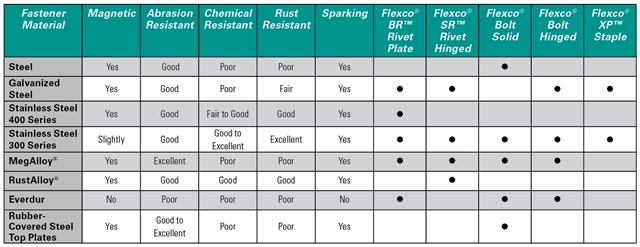
Still not sure?
There are a lot of factors that go into deciding what fastener to use for your application, and we’ve only touched on a small bit here. If you’re still stumped, we invite you to check out the “Help Me Choose” button on our each of our fastener line pages. And as always, stay tuned for more blogs on fastener selection by subscribing to our blogs here.
Authored by: Russ Heintz, Training and Technical Specialist
Russ Heintz has been with Flexco since 1995, working in various roles within the company before becoming Training and Technical Specialist. In this role, Heintz focuses on the efficiency of our products through in-house and field testing. Heintz also regularly conducts classroom and hands-on, internal or on-site training with Flexco employees, distributors, and customers.