It’s no surprise that keeping your belt clean to comply with regulatory standards whilst trying to maximise conveyor uptime is one of the biggest challenges faced in the food processing industry. However, ensuring you have the right processes and products implemented in your system can save you hours of productivity and significantly reduce labor costs spent on clean up.
Why conveyor belt sanitisation is important
According to a report by Food Safety Australia, there is an estimated 5.4 Million cases of foodborne illness per year in Australia alone.In a typical food production line, raw ingredients and processed products are transported along a belt conveyor system, exposing the system to risk of contamination. Other contamination issues can stem from areas that are inaccessible without removing the belt. Here, product debris can accumulate and provide a growth medium for bacteria. Keeping a sanitary conveyor not only ensures you stay compliant with Food Standards Australia New Zealand (FSANZ) but typically results in increased uptime and productivity, turning higher profit and reducing the manpower required.
How an unsanitary conveyor belt can affect your productivity
Unsanitary conveyor belts don’t only pose a risk of contamination and buildup of bacteria, but they also create a number of issues that can cost the conveyor significant downtime and lost productivity. These issues include product carryback and mistracking, which can then lead to belt damage and creates the ideal conditions for bacteria growth. These problems can also result in product falling from the belt and becoming waste.
So, how do I fix the problem?
Rectifying sanitation issues on your belt conveyor system can be solved a number of different ways, including taking a closer look at your belt conveyor components. Mechanical belt fasteners tend to be overlooked when discussing sanitation even though the right ones can actually make belt cleaning and sanitation quicker and easier. Let’s take a look!
- Common Bar Wire Hooks
Wire Hook Fastening Systems offer a low profile and cost effective belt splicing option across a number of industries and applications. Advantages of a the wire hook system include a low profile design, quiet operation, quick installation and a hinged connection making belt removal simple when cleaning or undergoing maintenance. As well as these, Clipper® and Anker® Wire Hook Fasteners should be considered as viable options, both of these share similar features to the common bar wire hook but also offer a constantly compressed style, creating a low profile, uniform design.
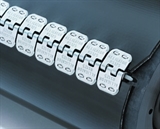 |
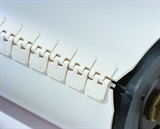 |
Flexco Alligator® Staple Fasteners |
Flexco Alligator® Plastic Rivet Fasteners |
- Clipper® or Anker® G Series™ Fastening Systems
Both the Clipper® and Anker® G Series™ Fastening Systems offer a low-profile splice and quickly removable hinge pin, making removal for sanitation easy. The Anker G Series Fastening System provides constant compression, resulting in a flat, uniform splice. The staggered-leg design with four alternating leg lengths deliver additional strength and durability to the finished splice. The Clipper G Series Fastening System offers a variety of different leg and point lengths, metal gauges, and strip lengths to meet your individual application needs.
More tools to keep your conveyor belt clean
To further reduce time during the conveyor sanitation process, food production facilities install Food Grade Primary Cleaners and Food Grade Secondary Cleaners. Doing so will dramatically reduce the carryback of material that can built up on those “hard to reach places,” thus further reducing conveyor sanitation times. You can read more about this in our blog titled: “What are your light-duty conveyor belt cleaners costing you?”
How does choosing the proper belt conveyor belt fastener benefit you?
It’s no secret that working towards increased conveyor uptime and a reduction of product waste and expenses is a common industry goal, but achieving this isn’t always a clear process. However, no-matter what the process involves, keeping a sanitary belt conveyor system will only benefit your site.
This benefit was recently seen in a food processing plant where over seven hours a night was being spent sanitising belts to keep up with U.S. Food and Drug Administration (FDA) compliance standards. Belt wear on the underside also meant belts needed to be replaced every six months. All of these factors led to a substantial loss of productivity and cost the plant hours of labor.
With a timeframe set by the FDA to fix their cleaning process, the plant had to implement changes. The incorporation of Alligator® Plastic Rivets allowed the plant to quickly remove the hinge pin and clean both the topside and underside of the conveyor belt, while also providing easier access to clean the conveyor structure and components. By doing this, the conveyor saw a reduction of belt mistracking and material loss, reducing cleaning time and manpower by 50 percent, and gaining three hours of production time each day.
To create a success story of your own, get in touch with the Flexco team to see how you could incorporate a Flexco Mechanical Belt Fastening System onto your conveyor and stop unsanitary practices for good.
Make the move to more sanitary conveyor belts today!
Ready to make the move towards more sanitary belts, or still not sure where to start? Request a free assessment or send us a message here.
Authored by: Laurie Shorten, National Light-Duty Product Manager
Shorten began working with Flexco in 2010 as Australia and New Zealand’s Light-Duty Product Manager. Prior to working with Flexco, he worked for 16 years at a light-duty belt conveyor company, making him well-equipped to handle the position of National Light Duty Product Manager.