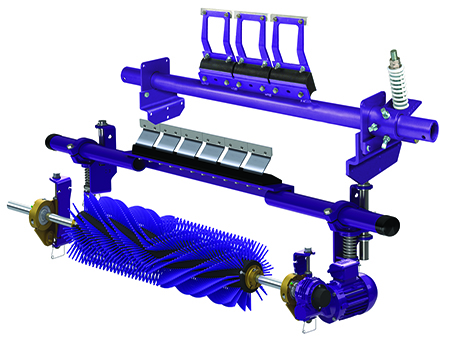
Industry
Auto glass Application Batch conveyor
Product
• HV Precleaner
• FMS Medium-Duty Secondary Cleaner with V-Tips
• Motorized Brush Cleaner
Objective
Reduce carryback
Conveyor Detail
30” wide, ½” thick 2-ply belt
Problem:
Several problems led to a complete overhaul of belt cleaners at an auto glass manufacturer in the Midwest. The existing polyurethane cleaners were having trouble cleaning static-induced carryback, and excessive dust from the carryback hitting each return roller was clouding the conveyor tunnel. A dedicated 1/2” airline was running at 80 psi all day and all night for a vibrator that was mounted on a dribble chute in order to move the carryback down to the chute at a yearly air-compressor operation cost of $3,000. Operators also found themselves positioning wheelbarrows under each return roller to catch the carryback that was falling off the belt, with a yearly cleanup cost estimate sitting at $10,000.
Solution:
After assessing the situation, the Flexco team advised the maintenance team to remove all the polyurethane cleaners and replace them with carbidetipped cleaners to avoid causing more static on the belt. A combination of the HV Precleaner, FMS Medium-Duty Secondary Cleaner with V-Tips, and Motorized Brush Cleaner was suggested. An unconventional solution for driving the brush cleaner was also suggested when the options of a motor or head pulley were taken off the table. Instead, a hold roller, with the brush shaft slave driven off the hold down roller shaft, was utilized.
Result:
Results were immediate as a visual inspection revealed that carryback was reduced approximately 85% - a significant improvement. This also reduced the amount of time and money spent cleaning up the carryback. Additionally, the air supply to the vibrator was reduced to 10 psi, and is on a timer that runs for short periods of time at intervals, slashing compressor costs. Finally, the unconventional hold down roller method suggested by Flexco and its distributor partner worked well. The customer was impressed with the fact that with hard work, a solution was found even when a product wasn’t readily available to solve the problem.